Product Search
Quickly find the product you need
Products List
Refractory Knowledge
- Thermal Shock Resistant Fireproof Heat In
- Classification of mullite insulation bric
- Manufacturing process of fire clay insula
- Refractory material production process
- Aggregates Used For the Production of Ins
- Production Process Methods of Refractory
- Pollution and treatment in the production
- the development of the refractory brick i
- The Use of Mullite Insulation Bricks
- Pros and cons of lightweight mullite bric
Products List
- Phone:0086-370-63838939
- Email:sales@sunriserefr.com
- Office Address: No.36 Fengchan Road Of Zhengzhou, Henan, China (Mainland)
The Production And Application Of High Alumina Insulation Brick
Date:2015-11-03 00:51 | From:Zhengzhou Sunrise Refractory | Author:admin
High alumina insulating bricks are also known as high alumina heat insulating bricks. It is a new type of lightweight insulating material which contains approximately 48% alumina,mullite and glass phase or corundum.
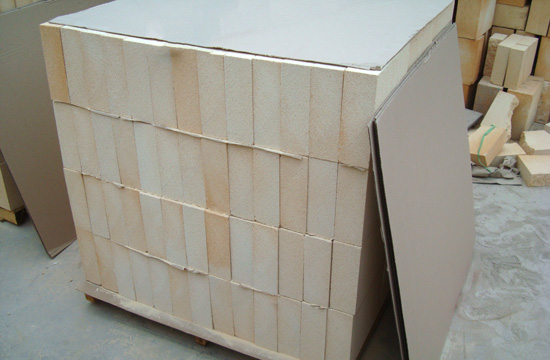
High alumina insulating brick mainly uses bauxite and binding clay as raw materials with binders and sawdust. In order to improve the performance, industrial alumina, corundum, sillimanite, kyanite and silica powders are added to obtain products with different densities and service temperature. Generally its service temperature is 1250~1350℃, sometimes 1550℃.
High alumina insulating brick is generally made by the foam method. Its bulk density is between 0.4~1.0g/cm3. Sometime it is made by adding ignition loss substances to improve its porosity.
The foam method includes the preparation of foam agent, formulation of foam slurry, formation, drying and firing.
(1)The preparation of foam agent
Foam agent is actually a surfactant. The commonly used foam agent is rosin soap. The rosin soap is added to the hot glue and stirred to form foam agent. Alum and aluminum sulfate are used as foam stabilizers.
(2)The formulation of foam mud
Mix binding agent, bauxite and sawdust according to the formulation to make mud. The mix the mud and foam agent in a blender to make foam mud. The ratio of the mud and foam agent depends on the bulk density of the products.
(3)Formation
High alumina brick is formed by casting moulding. The mould can be wood or metal. The working surface of the mould should be smooth and coated with lubricants. Put the mould on the drying board and cast foam mud slowly to avoid the generation of large bubbles.
(4) Drying
After casting the products with mold are dried at about 40℃ for 18-20h. When the gap between the product and mould becomes 3-5mm, release the product from the mould. Continue to dry it at 80-90℃. If dried in a tunnel kiln, the inlet temperature should not exceed 40 ℃ and the outlet temperature should not exceed 150 ℃. Drying is a key step. If not controlled properly, there will be cracks, crispy bottom, concave heart, membrane adhesion and broken corners.
(5)Firing
Determine the loading position and the maximum firing temperature. The maximum firing temperature is generally 1320-1380℃. The insulation time is 5-8h. The higher the content of Al2O3, the higher the maximum firing temperature, sometimes even 1580-1620℃.
It hold the most stable and lowest thermal conductivity of all insulating refractory bricks at present. Since it is light, the total weight of the furnace body and walls thickness can be reduced effectively. Thermal efficiency and working condition can be improved,energy consumption can be lowered,productivity and significant economic results can be achieved. When directly contacting the flame, the surface contact temperature generally should not exceed 1350℃.
High alumina insulation brick can be used in insulation layers and parts without erosion by high temperature molten materials. It is widely used in lining or insulating layers of various industrial furnaces, and kilns in petrochemical, machinery, ceramic industry, such as lining and insulating layer of high temperature kilns.--carbon black stove, gasifier, hydrogen manufacturing furnace and shuttle kiln,etc.