Product Search
Quickly find the product you need
Products List
Refractory Knowledge
- Production Process Methods of Refractory
- the development of the refractory brick i
- Classification of mullite insulation bric
- Thermal Shock Resistant Fireproof Heat In
- Pros and cons of lightweight mullite bric
- Manufacturing process of fire clay insula
- Refractory material production process
- Pollution and treatment in the production
- Aggregates Used For the Production of Ins
- The Use of Mullite Insulation Bricks
Products List
- Phone:0086-370-63838939
- Email:sales@sunriserefr.com
- Office Address: No.36 Fengchan Road Of Zhengzhou, Henan, China (Mainland)
How to Make Fire Clay Inuslation Brick
Date:2015-11-11 19:25 | From:Zhengzhou Sunrise Refractory | Author:admin
Fie clay insulation brick is a kind of light wieght insulation material containing 30%-48% Al2O3. It can be used to make high temperature insulation, ultra-high temperature insulation filler, high temperature refractory lightweight aggregate concrete and high temperature castable.
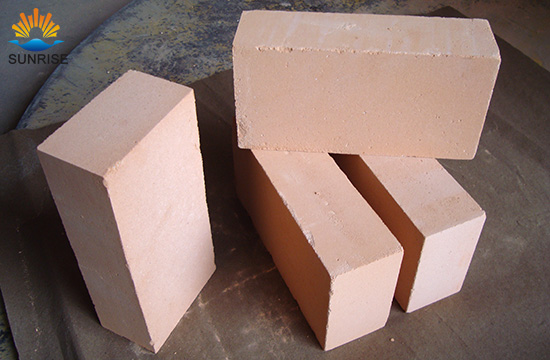
Fie clay insulation brick is made of refractory clay, cenosphere and refractory clay clinker with addition of binders and sawdust by formulating, mixing, molding, drying and firing. Its output accounts for more than half of the whole output of insulation bricks.
Fire clay brick is genetrally made by adding cenosphere or foam. Cenoshpere should contain more than 30% Al2O3 and less than 3% Fe2O3. It is a type of closed hollow sphere, with thin shell and high strength. Its has white color. Its bulk density is 0.38~0.44g/cm3. Its particle size is 20~250μm and most are 50 ~ 150μm. Whole bead ratio is more e than 95%. Cenposphere is added according to the bulk density, generally 10%-70%. The lower the bulk density is, the more cenosphere is added. Clay clinker powder is added to reduce the volume shrinkage of cenosphere.
Clinker powder and cenospheres are barren aggregates. Cenoshpere is round or nearly round, with smooth surface, fine particle and large specific surface area. It requires binding agents to have good binding properties. The main binding agent used include refractory clay, sulfite pulp waste, aluminum sulfate, sodium silicate, phosphoric acid and phosphate, dextrin and resin. Refractory clay is cheap and abundant with higher binding ability, dispersion, plasticity, fire resistance and sintering properties, wo it is used most widely. According to the type, bulk density and technical requirements, an appropriate amount of organic or inorganic binders are added.
Sawdust should be screened. The particle size should be less than 1 ~ 2mm.
Mix the raw materials uniformly. There are two methods. One way is to add cenosphere, sawdust, binders, water, clay and clinker powder in order. Knead for 5-6min to obtain mud materials with cenosphere or sawdust as the core, wrapped with a layer of binders and clay and the outermost layer of dry powder. Another way is to cenosphere, clinker powder, clay and sawdust into the machine. Then after dry mixing the materials for 2-3min, add water and binders and wet mix the materials for 3-4min. Mud can be moulded after aging for 12-24h. the water content of the mud depends on the bulk density, indredient ratio and moulding method, genenrally 20%-30%.
The products are usually moulded by hand or machine. The moulding machine should be 150-300kN brick press. After moulding the brick has low strength and should be handled with care.
Then bricks are dried in a tunnel drier or a pit. The inlet temperature of the tunnel drier should not exceed 50℃ and the outlet temperature should not exceed 150℃. After drying, the content of residual water should be controlled under 2%.
When firing, the bricks should be side loaded. The bricks should be laid flatly, steadily and straightly. Rice husk is paved between layers. Joints should be reserved between bricks. The loading height is generally 1.5-1.8m. For products with bulk density of less than 0.6g/cm3, it should not exceed 1.2m and the bricks should be loaded in the low temperature areas. The temperature should be even and the maximum firing temperature depends on the cenosphere, the quality of clay and the bulk density. For products with a bulk density of 0.4-0.6g/cm3, the maximum temperature is 1220-1250℃. For products with a bulk density of 0.8-1.0g/cm3, the maximum temperature is 1250-1280℃. In actual production, products with different bulk densities are often fired in the same kiln. According to the temperature distribution, diffferent products are loaded in different parts in order to improve the firing quality.
Fire clay insulation brick finds a wide application in many fields. It is mostly used in the insulation layer of thermal equipment and industrial furnaces, areas without severe erosion by molten materials and refractory coating in direct contact with flame.