Product Search
Quickly find the product you need
Products List
Refractory Knowledge
- Refractory material production process
- the development of the refractory brick i
- Production Process Methods of Refractory
- Manufacturing process of fire clay insula
- Classification of mullite insulation bric
- Thermal Shock Resistant Fireproof Heat In
- Aggregates Used For the Production of Ins
- Pros and cons of lightweight mullite bric
- The Use of Mullite Insulation Bricks
- Pollution and treatment in the production
Products List
- Phone:0086-370-63838939
- Email:sales@sunriserefr.com
- Office Address: No.36 Fengchan Road Of Zhengzhou, Henan, China (Mainland)
Classification of Insulation Bricks
Date:2015-10-23 23:03 | From:Zhengzhou Sunrise Refractory | Author:admin
Insulation brick is a type of light weight porous shaped refractory that is processed into a specific shape before use. It has stable performance and is convenient to use, transport and restore.
Insulation brick is conventionally made by a general manufacturing method in which a refractory clay is added to a highly refractory aggregate such as alumina, alumina silica, silicic acid, magnesia or zirconia, and to a pore making granular combustible substance such as wood chips, foamed polystyrene or coke. Sufficient water is added to the mixture and then the mixture is kneaded or mixed, and is extruded, pressed or cast into bricks. The cast bricks are then dried and fired as required.
According to the chemical composition, insulation bricks can be mainly divided into fire clay insulation brick, high alumina insulation brick, mullite insulation brick, silica insulation brick, and diatomite insulation brick.
Fire Clay Insulation Brick
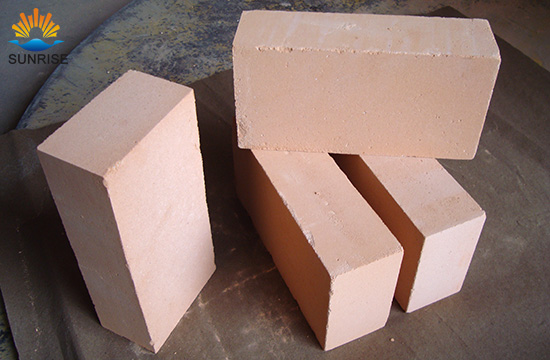
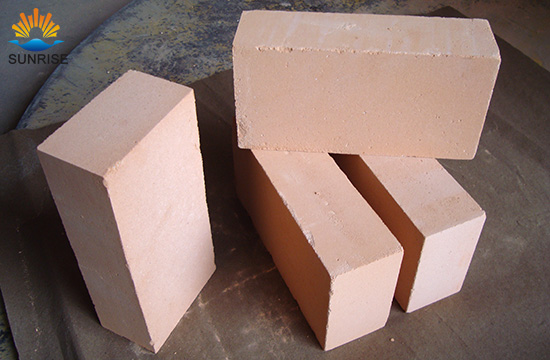
Fire clay insulation brick refers to the light weight refractory containing 30%-60% Al2O3. It is usually fired at about 1300℃. Commonly used fire clay insulation brick has a bulk density 0.55-1.5g/cm, cold crushing strength 1.5-6MPa, thermal conductivity 0.2-0.4W/(m·K) and max service temperature 1200-1400℃. It is widely used in the insulation layers that do not directly contact with molten material and corrosive gases in various furnaces.
High Alumina Insulation Brick
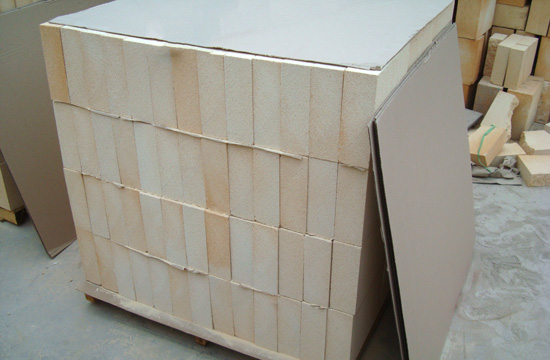
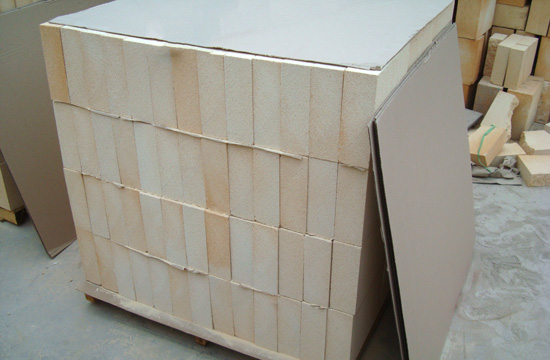
High alumina insulation brick is a type of light weight refractory containing more than 45% Al2O3. It is usually made by adding foaming agent and firing at 1350-1500℃. It is apparent porosity is about 70%. It has a bulk density 0.4-1.3g/cm, cold crushing strength 1.3-8.1MPa, thermal conductivity 0.3-0.6W/(m·K) at 350℃ and max service temperature 1350-1800℃. It has high refractoriness and good thermal shock resistance and good stability in the reducing atmosphere. It can directly contact with flame and is generally used in the insulation layer of furnaces.
Mullite Insulation Brick
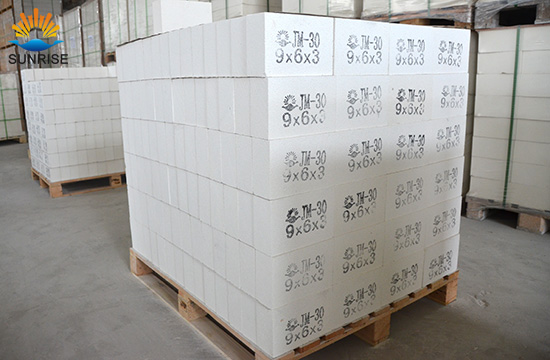
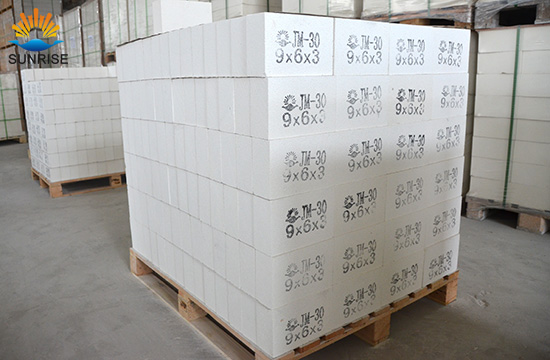
Mullite insulation brick is a type of light weight refractory with mullite as its main crystal phase and 50%-85% Al2O3. Since it has excellent high temperature mechanical property and chemical stability, it has good high temperature strength, good creep resistance, low thermal expansion coefficient and good resistance to chemical attack and thermal shock. It can directly contact with flame. Depending on the Al2O3 content and bulk density, it can used at 1350-1650℃.
Besides of the three types of insulation bricks above, silica insulation brick and diatomite insulation brick are also used for the insulation of furnaces. The atmosphere, the environment and the operating characteristics should be taken into consideration when selecting insulation bricks.