Product Search
Quickly find the product you need
Products List
Refractory Knowledge
- Classification of mullite insulation bric
- Manufacturing process of fire clay insula
- Pollution and treatment in the production
- Thermal Shock Resistant Fireproof Heat In
- The Use of Mullite Insulation Bricks
- the development of the refractory brick i
- Production Process Methods of Refractory
- Aggregates Used For the Production of Ins
- Refractory material production process
- Pros and cons of lightweight mullite bric
Products List
- Phone:0086-370-63838939
- Email:sales@sunriserefr.com
- Office Address: No.36 Fengchan Road Of Zhengzhou, Henan, China (Mainland)
Characteristics and application of silica brick refractory products
Date:2020-02-13 15:06 | From:Zhengzhou Sunrise Refractory | Author:admin
Silica brick refers to refractory products with SiO2 content above 93%.
The higher the SiO2 content in the silica raw material, the higher the fire resistance of the product. K2O.Na2O and other impurities are harmful and will seriously reduce the fire resistance of refractory products. Impurities such as Fe2O3, CaO, and MgO act as fluxes. The raw materials of high-grade silicon brick need special treatment to remove impurities.
The mineral composition of silica brick is coexisting multiphase structure such as scaly quartz, cristobalite, a small amount of residual quartz, and glassy material formed at high temperature. The mineral composition fluctuates greatly depending on the silicon brick production process and the nature of the raw materials used.
Silica brick is an acid refractory material, which has a strong resistance to acidic slag or acidic molten metal erosion, but has a poor resistance to the erosion of alkaline substances, and is easily damaged by the action of oxides such as Al2O3, K2O, and Na2O. FeO, Fe2O3 and other oxides have good resistance.
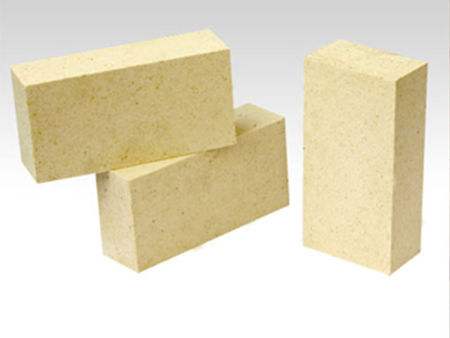
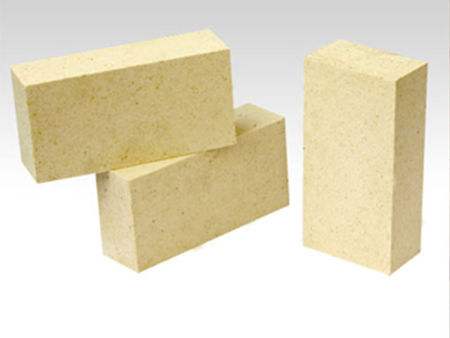
A higher softening temperature under load is an excellent characteristic of silicon bricks, which is generally 1640 to 1680 ° C, which is close to the melting point of scaly quartz (1670 ° C) and the melting point of cristobalite (1713 ° C). The volume of silicon brick is stable in the range from 300 ℃ to close to the melting point (scaly quartz or cristobalite). When it is used, it will have a volume expansion of about 1.5% to 2.2% when heated to 1450 ℃, which is good for ensuring the structure of masonry. Strength and air tightness.
The biggest disadvantage of silica brick is its poor thermal shock resistance (the number of water-cooling cycles is generally 1 to 4 times), followed by the low fire resistance (generally 1690-1730 ° C), and its application range has been greatly limited.
Silicon brick is mainly used for the carbonization chamber, combustion chamber and partition wall of coke oven (about 73% of refractory materials for coke oven are silicon brick), glass pool kiln and kiln roof, pool wall, high temperature bearing parts of hot air furnace , Carbon furnaces and other thermal furnaces. In order to increase the production capacity of modern large-scale coke ovens, it is necessary to thin the coke oven carbonization chamber, the combustion chamber and the partition wall, so it is required to use high-density and high thermal conductivity silicon brick.
If you are interested in our fused azs bricks, or need other types of refractory materials, please contact our Tianyang Refractory Group, we will definitely provide you with the best quality refractory materials and the most reasonable quotation.