Product Search
Quickly find the product you need
Products List
Refractory Knowledge
- Pros and cons of lightweight mullite bric
- Aggregates Used For the Production of Ins
- The Use of Mullite Insulation Bricks
- Classification of mullite insulation bric
- the development of the refractory brick i
- Production Process Methods of Refractory
- Pollution and treatment in the production
- Manufacturing process of fire clay insula
- Thermal Shock Resistant Fireproof Heat In
- Refractory material production process
Products List
- Phone:0086-370-63838939
- Email:sales@sunriserefr.com
- Office Address: No.36 Fengchan Road Of Zhengzhou, Henan, China (Mainland)
Lightweight corundum brick production process and features
Date:2018-06-04 16:13 | From:Zhengzhou Sunrise Refractory | Author:admin
Lightweight corundum brick is made of alumina with more than 90% of industrial alumina as raw material, plus a small amount of soft clay and binder, and grinded into slurry together. It adopts foam method or gas generation method, and is casted and dried at 1400. ~1550 °C fired lightweight refractories. It is characterized by high refractoriness, high compressive strength, low re-burn volume shrinkage, low thermal conductivity, and good resistance to thermal shock.
The raw materials of lightweight corundum bricks are ground in a silicon-lined mill. The main residual material is SiO2. Due to the addition of sintering additive TiO2 in the clinker of semi-light corundum bricks, other impurities are added from raw materials and yam. The content of Fe2O3, Na2O, CaO, MgO, etc. entering the material is not large. The light corundum brick manufactured by the casting method and the gasification method is required to contain a certain amount of CaO, especially in the form of lime, gypsum or high-alumina cement. Bricks, occasionally added with MgO or P2O3. The bricks containing P2O3 are manufactured by gas foaming. After the mud was treated with hydrochloric acid, the CaO and P2O3 impurities were removed and the Al2O3 content was increased to 99%, which significantly improved the refractory properties of the firebrick.
The main crystal phase of the lightweight corundum refractories is an equiaxed corundum crystal with a size of 8 to 40 μm. The bonded portion is a fine corundum and a few glassy phases. The lightweight corundum brick manufactured by the alumina-sawdust pulverized casting and the introduction of CaO in the gas foaming method, the binding portion containing calcium hexaaluminate, and the introduction of phosphoric acid; has calcium phosphate and aluminum phosphate dissolved simultaneously in hydrochloric acid.
For all lightweight corundum bricks, the generation of porosity is a method-based transfer, and most of the pores constitute open pore systems.
The compactness of lightweight corundum refractories depends on the method of manufacture. For example, it is impossible to increase the porosity of the brick to 65% by the method of burning mash, 18.5 AFS for the brick of the additive method for burning moromi, and 16.5 AFS for the foam brick.
The method of burning mash, which includes the porosity and density of light-weight corundum refractories made from alumina and sawdust, is basically dependent on the amount of additives (coke, sawdust) and the particle size is slightly smaller. Alumina. The porosity and density of the foamed lightweight corundum refractories mainly depend on the amount of foam generated and the moisture of the loach.
The porosity and density of the lightweight corundum refractories produced by the foaming method basically depend on the optimum quantity of the additives capable of violently precipitating gas and the nature of the mud, and the addition of light-weight cohesive structures when vigorous gassing occurs. Quantity of goods. While reducing the density, the use of calcined and ground alumina was promoted. When the density decreased from 1.23 g/cm3 to 0.9 g/cm3, the porosity increased from 67.2% to 76.4%, and the calcined alumina increased from 10% to 100%.
Improve the porosity of lightweight corundum refractory bricks, and the deformation temperature is significantly reduced.
The thermal conductivity of the sintered corundum refractories is much lower than that of the foamed corundum bricks. Light-weight corundum refractories have lower thermal conductivity in vacuum than dense bricks. One of the reasons for this is the decrease in the thermal conductivity of the gas, and secondly, the reduction of the contact surface in the brick. The thermal conductivity of the lightweight lightweight refractories in hydrogen is also greatly enhanced. At an average temperature of 800°C, the thermal conductivity of the lightweight corundum refractories is increased by 60%, and its temperature dependence does not change. ·
Porous lightweight bricks, when the other conditions are the same, below 600-700°C, have higher thermal conductivity than large bricks; when the temperature exceeds 600-700°C, the opposite is true.
Since the thermal conductivity and strength of lightweight bricks are lower than that of compact bricks, their thermal shock resistance is also significantly reduced, and the greater the porosity, the more the reduction. Bricks burning cerium additives, in particular adding granular materials, have better thermal shock resistance than foam lightweight bricks. However, a large quantity of lightweight corundum refractory bricks (230mm×120mm×65mm) of standard size are heated to 1300°C, and the equipment withstands. 1-2 heat exchanges, it is difficult to adapt to the conditions of use. At the same time, it is confirmed that the formation of cracks in the initial stage of cooling and the increase in the volume of broken parts increase the heat insulation performance of lightweight corundum fire bricks.
The semi-light corundum bricks sintered at 1750°C with a porosity of 39% to 42% have a residual shrinkage of 0.52% to 1.8% after being reburned at 1750°C for 3 hours; the foams and burned yttrium additives produce light weight. Corundum brick, after 1740 °C, 2h re-burn residual shrinkage of less than 0.5%. The firing temperature of the refractory bricks reaches 1520 to 1580°C, and the residual shrinkage increases. After 1550°C., 2h reburning shrinks 1% to 2%; while at 1750°C,, 2h burns shrink to 2% to 8%. .
The lightweight corundum bricks can be used for thermal insulation of thermal equipment at high temperatures, or lining with thermal equipment that directly affects the flame, but should not be used for direct erosion of slag. Use in a reducing atmosphere also has a higher stability. The maximum use temperature is generally up to 1650°C, and high purity products can reach 1800°C.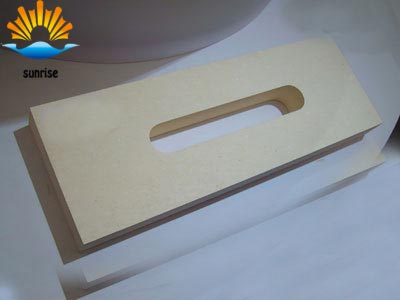
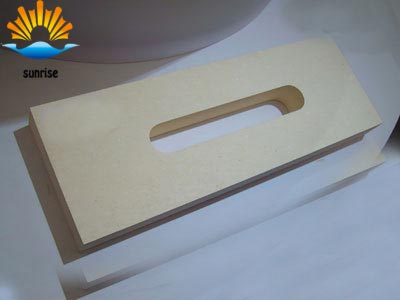