Product Search
Quickly find the product you need
Products List
Refractory Knowledge
- Production Process Methods of Refractory
- Refractory material production process
- Pros and cons of lightweight mullite bric
- the development of the refractory brick i
- Pollution and treatment in the production
- Aggregates Used For the Production of Ins
- The Use of Mullite Insulation Bricks
- Thermal Shock Resistant Fireproof Heat In
- Manufacturing process of fire clay insula
- Classification of mullite insulation bric
Products List
- Phone:0086-370-63838939
- Email:sales@sunriserefr.com
- Office Address: No.36 Fengchan Road Of Zhengzhou, Henan, China (Mainland)
Extrusion type thermal insulation brick
Date:2018-04-28 15:49 | From:Zhengzhou Sunrise Refractory | Author:admin
The advantage of lightweight high thermal insulation bricks is that they have a large number of holes, multiple rows of holes, and thin hole walls, which are the main factors that have high thermal insulation properties. The disadvantage of this type of brick is its low compressive strength. The perforated brick kilns have to obtain certain thermal insulation properties. The meticulous design of its hole arrangement and hole shape will affect the compressive strength of the perforated brick. The German Brick and Tile Research Institute used compression molding to produce high thermal insulation bricks. However, there is a certain demand for thermal insulation bricks extruded from the construction market.
For many years people have devoted themselves to the research of microporous ceramic bodies. Its purpose is first of all to produce panels with high thermal insulation properties. This has led to the development of porous clay porous bricks containing micropores. The strength of these bricks is between 2 and 4 N/mm2.
The perforated bricks were tested for compressive strength based on the user's disagreement with the load requirements of the perforated bricks. The incorporation of pore-forming agents generally lowers the compressive strength of the green body and the degree of influence is also related to the type of pore-forming agent and the size of the pore-forming agent particles. The pore-forming agent test and its treatment method also directly affect the forming, drying and baking of the porous brick. The bulk density of the perforated bricks can be controlled to a lower level by proper pretreatment of the raw materials and the addition of fine porogens.
Reasonable clay porous brick production process can effectively offset the reduction of compressive strength. The structural strength of porous bricks depends primarily on the primary mineral composition of the raw bricks and the raw materials that are incorporated. The incorporation of fuel can reduce the strength of the brick and the degree of reduction is primarily related to the size and shape of the fuel particles. The condition of some additives to increase the strength of bricks is more complicated. It will change the sintering state of the bricks during the roasting process to form some new matrix, thereby increasing the structural strength of the bricks, mineral additives such as lime, chalk and industrial wastes. In order to obtain the optimum composition, it is necessary to incorporate some of the above pore formers into the raw brick material. The geometric shape of the perforated brick hole wall is the main factor affecting the strength of the brick. The size and number of the micro holes in the brick and the density of the micro holes are also the main factors affecting the strength of the brick. The thickness of the material between the two pore forming agent particles affects the strength. The most obvious. The large accumulation of a plurality of pore former particles such as large polystyrene particles increases the density and thermal conductivity of the brick article. Porous bricks incorporating pore-forming agent pore formers will leave tiny holes in the brick product after combustion.
Development of Microporous Porous Bricks
In order to produce microporous bricks using equipment and extrusion molding techniques common in the brick industry, the porogen-doped raw materials must be processed into an extrudable slurry. First, the raw material is made into a solid content slurry with a rapid stirrer. Stabilizer and pore-forming agent stabilizer are mixed during the stirring process of the slurry. The liquefaction effect can reduce the moisture content of the slurry and improve the slurry flowability. The mixing of the agent thickens and thickens the slurry. Slurry and pore formers can also be injected simultaneously into a twin-shaft mixer for vigorous stirring until the desired consistency is achieved. The incorporation of dry materials will affect the uniformity of the extruded bricks, so the dry materials must be incorporated into a twin-shaft mixer. In order to obtain a low bulk density (0.4~0.5kg/dm3) of brick products, powdered straw, sawdust, and very fine polystyrene are required; the incorporation of powdered lime or clay can produce higher density (0.7 ~0.8kg / dm3) brick products. The use of a modified brick machine that does not require vacuum, the molding pressure does not need to be too high. Although the porosity of the micropores is high, porous bricks with a porosity of 50% can still be produced. The production of this porous brick with high porosity, high porosity, and high-precision structure is of practical value. Figure 1 shows high porosity porous microporous bricks being extruded.The advantage of lightweight high thermal insulation bricks is that they have a large number of holes, multiple rows of holes, and thin hole walls, which are the main factors that have high thermal insulation properties. The disadvantage of this type of brick is its low compressive strength. The perforated brick kilns have to obtain certain thermal insulation properties. The meticulous design of its hole arrangement and hole shape will affect the compressive strength of the perforated brick. The German Brick and Tile Research Institute used compression molding to produce high thermal insulation bricks. However, there is a certain demand for thermal insulation bricks extruded from the construction market.
For many years people have devoted themselves to the research of microporous ceramic bodies. Its purpose is first of all to produce panels with high thermal insulation properties. This has led to the development of porous clay porous bricks containing micropores. The strength of these bricks is between 2 and 4 N/mm2.
The perforated bricks were tested for compressive strength based on the user's disagreement with the load requirements of the perforated bricks. The incorporation of pore-forming agents generally lowers the compressive strength of the green body and the degree of influence is also related to the type of pore-forming agent and the size of the pore-forming agent particles. The pore-forming agent test and its treatment method also directly affect the forming, drying and baking of the porous brick. The bulk density of the perforated bricks can be controlled to a lower level by proper pretreatment of the raw materials and the addition of fine porogens.
Reasonable clay porous brick production process can effectively offset the reduction of compressive strength. The structural strength of porous bricks depends primarily on the primary mineral composition of the raw bricks and the raw materials that are incorporated. The incorporation of fuel can reduce the strength of the brick and the degree of reduction is primarily related to the size and shape of the fuel particles. The condition of some additives to increase the strength of bricks is more complicated. It will change the sintering state of the bricks during the roasting process to form some new matrix, thereby increasing the structural strength of the bricks, mineral additives such as lime, chalk and industrial wastes. In order to obtain the optimum composition, it is necessary to incorporate some of the above pore formers into the raw brick material. The geometric shape of the perforated brick hole wall is the main factor affecting the strength of the brick. The size and number of the micro holes in the brick and the density of the micro holes are also the main factors affecting the strength of the brick. The thickness of the material between the two pore forming agent particles affects the strength. The most obvious. The large accumulation of a plurality of pore former particles such as large polystyrene particles increases the density and thermal conductivity of the brick article. Porous bricks incorporating pore-forming agent pore formers will leave tiny holes in the brick product after combustion.
Development of Microporous Porous Bricks
In order to produce microporous bricks using equipment and extrusion molding techniques common in the brick industry, the porogen-doped raw materials must be processed into an extrudable slurry. First, the raw material is made into a solid content slurry with a rapid stirrer. Stabilizer and pore-forming agent stabilizer are mixed during the stirring process of the slurry. The liquefaction effect can reduce the moisture content of the slurry and improve the slurry flowability. The mixing of the agent thickens and thickens the slurry. Slurry and pore formers can also be injected simultaneously into a twin-shaft mixer for vigorous stirring until the desired consistency is achieved. The incorporation of dry materials will affect the uniformity of the extruded bricks, so the dry materials must be incorporated into a twin-shaft mixer. In order to obtain a low bulk density (0.4~0.5kg/dm3) of brick products, powdered straw, sawdust, and very fine polystyrene are required; the incorporation of powdered lime or clay can produce higher density (0.7 ~0.8kg / dm3) brick products. The use of a modified brick machine that does not require vacuum, the molding pressure does not need to be too high. Although the porosity of the micropores is high, porous bricks with a porosity of 50% can still be produced. The production of this porous brick with high porosity, high porosity, and high-precision structure is of practical value. Figure 1 shows high porosity porous microporous bricks being extruded.
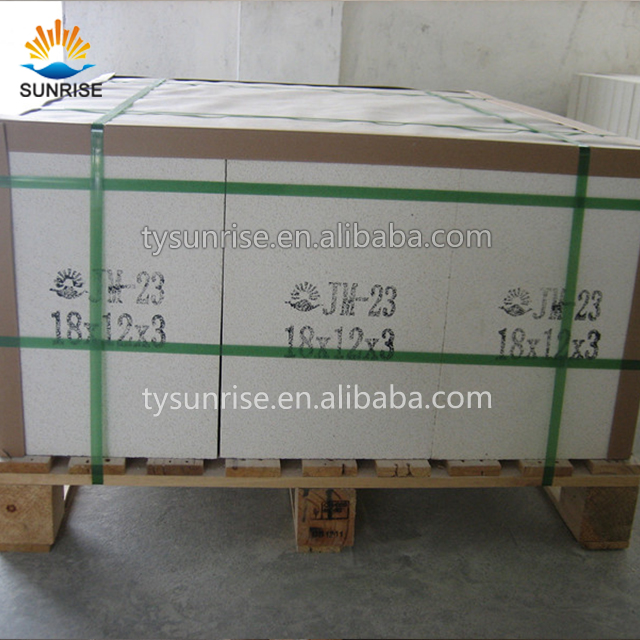
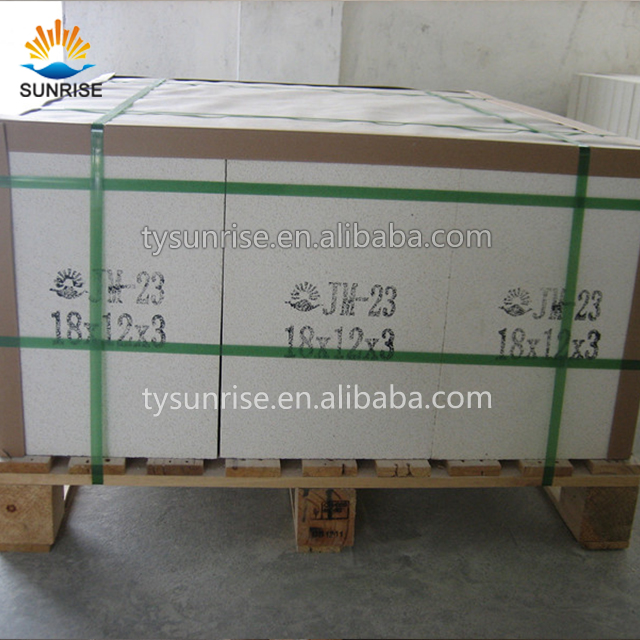